Primary, secondary and tertiary packaging: characteristics and functions
Primary, secondary and tertiary packaging: characteristics and functions
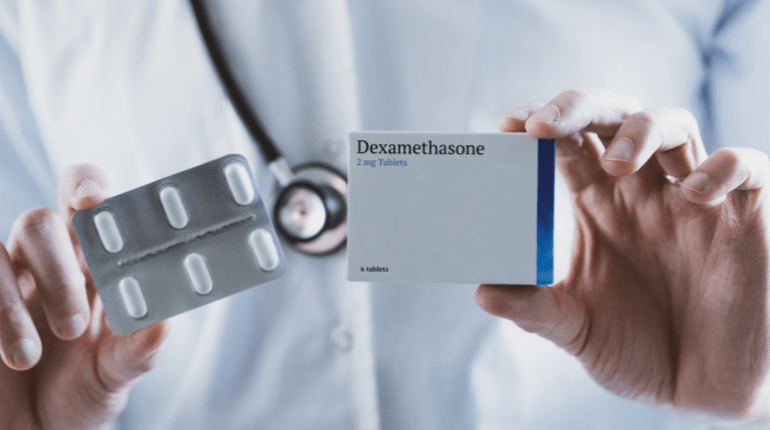
Pharmaceutical packaging plays a crucial role throughout the entire distribution chain. A pharmaceutical company has to select designs, materials, storage and transportation solutions to optimise supply costs and comply with international regulations. The packaging requirements for a product are defined in European Directive 2004/12/EC on packaging and packaging waste, which modifies and supplements Directive 94/62/EC. In this text, the packaging is classified into three categories: “primary,” “secondary” and “tertiary,” each serving a different function and purpose. The choice of these three packaging levels becomes a strategic factor.
Primary Packaging
Primary packaging is in direct contact with the product (examples include blister packs for tablets, bottles containing syrup, or sachets for powdered medication). It must be sterile (as well as the materials used to produce it) to prevent product contamination from external agents, light and air. For this purpose, primary packaging is made in “clean rooms”, under completely aseptic and controlled conditions. In addition, primary packaging must allow the clear identification of the medicine and facilitate its intake.
For this first level of packaging, the EU Directive 2004/12/EC has been supplemented by ISO 15378, which specifies the requirements for Quality Management Systems applied to materials used for the primary packaging of medicines to guarantee consumer safety and minimize risks.
Purified pharmaceutical glass, plastic and aluminium are mainly used in pharmaceutical packaging. Glass and cardboard are typically processed by different companies than those working with plastic because each material has distinct characteristics.
Glass has chemical and mechanical properties that provide high stability, resistance, and transparency.
Plastics play a central role in bottle, vial or pill container production because they allow personalised designs and protect sensitive medications. Although the pharmaceutical industry cannot yet do without the use of plastic yet, efforts are being made to find alternative solutions. Currently, sustainable choices adopted to minimize environmental impact are, for example, bio-plastics, recycled plastics, or new polymer materials mixed with organic compounds like thermoplastic resins.
Lastly, aluminium is widely used to produce blister packs. It is a flexible, insulating and highly customisable material.
Secondary Packaging
Secondary packaging is not in direct contact with the medicine, but Directive 2001/83/EC still establishes some strict production requirements, including aspects related to printing. Secondary packaging represents the next level after primary packaging, which is why it can only be produced after a study of the latter. Secondary packaging is designed to ‘physically’ protect primary packaging, in addition to:
- Protect individual units;
- Track the medicine through identification codes;
- Provide mandatory legal information (product name, pharmaceutical formula, expiration date, etc.);
- For over-the-counter (OTC) medications (those not requiring a prescription or hospital usage), promote the product through specific marketing-oriented designs that reflect the brand’s identity, capture consumer attention, and create a personalized customer experience from pharmacy displays. Exceptions are prescription pharmaceuticals or hospital medications: they reach healthcare professionals first and do not require marketing strategies for the consumer. Instead, they are regulated by European legislation based on Directive 2001/83/EC.
In secondary packaging, materials such as cellulose and carton are increasingly being used to simplify disposal and recycling, reduce environmental impact and minimize production costs.
Modern packaging solutions, like those offered by Eurpack, avoid excessive packaging materials (overpackaging) and use environmentally friendly and sustainable materials.
Eurpack specialises in secondary packaging, with extensive knowledge and field experience in complex supply chain dynamics. This specialization enables them to provide their customers with packaging solutions based on advanced and fast design. Eurpack’s solutions can assemble various elements into a single composition (boxes, leaflets, blisters, medical device components) to optimise storage and development times and costs.
Tertiary Packaging
With tertiary packaging refers to packaging designed to simplify the storage and transportation of goods. The functions of tertiary packaging include:
- Ensuring stability, safety, and protection against impacts;
- Optimising storage space in warehouses by utilising it efficiently;
- Facilitating the movement of goods;
- Enabling traceability of goods through material or product coding systems.
Unlike the first two levels of packaging, which play an essential role in the hands of the consumer or at a point of sale, tertiary packaging must be functional to improve logistics operations. Therefore, aesthetics is not relevant. The primary material used is typically micro-wave cardboard, made often in eco-friendly materials to reduce environmental impact, with neutral prints to avoid costs and emissions excessively.
During palletising, this kind of packaging does not waste space on pallets and avoids excessive weight during transportation. In Europe, some communities adopted storage standards, like the Europallet, a standardized size of the pallet (1,200×800 mm, with a maximum load capacity of 1,500 kg) wich optimizes the space used on pallets and speeds up the handling of loads.
The importance of relying on a specialised partner
The three levels of packaging mentioned above are part of a system in which each phase is linked to the previous one. Primary packaging is built around the product, secondary packaging is designed based on the primary packaging, and tertiary packaging takes into account the secondary packaging it will protect. Companies that manage a single packaging line, even if they are highly specialised, need to acquire information on the previous and subsequent production levels, to design customised solutions in a predetermined way and timeline without excessively impacting storage costs.
Therefore, it’s essential, for a company that would like to consider outsourcing its design packaging to find partners who have depth knowledge of the industry and the different packaging dynamics, which we have seen in this article to be strongly interconnected.