The importance of pharmaceutical packaging quality control
The importance of pharmaceutical packaging quality control
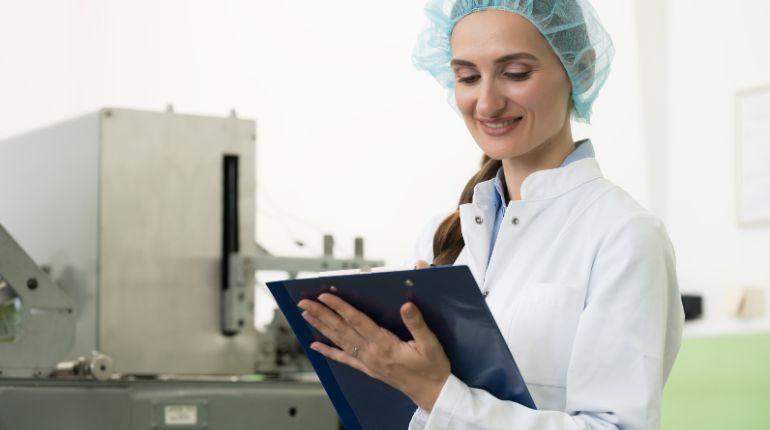
Pharmaceutical packaging is essential for maintaining product integrity, preventing contamination, and ensuring drug traceability throughout the supply chain. Quality control tests should be conducted at every stage of packaging design and development, from production to use for the packaging process in pharmaceutical companies, in compliance with international standards. In addition to meeting these regulations, quality-controlled and validated packaging is essential for optimizing economic resources, time, and productivity.
In this article, we will outline the fundamental quality requirements of secondary packaging and delve into some of the most crucial control tests that validate its introduction to the market.
GMP guidelines on pharmaceutical packaging quality control
The design of primary, secondary and tertiary pharmaceutical packaging adheres to many quality rules based on ISO and GMP (Good Manufacturing Practice) standards. GMP outlines different chapters of rules to follow in the production of medicines and their packaging. Packaging is essential for protecting pharmaceuticals from environmental factors such as light, moisture, and air, avoiding contamination and tampering, ensuring long-term preservation and preventing damage during transport along the logistics chain. Additionally, packaging provides clear information about its contents, validity, and the product’s origin to all stakeholders in the supply chain, right up to the consumer. Thanks to its clear and accessible design, end users can easily understand what they are purchasing and dispose of the packaging.
Pharmaceutical companies to obtain high performances of drugs, must conduct multiple quality tests in collaboration with suppliers and partners to validate the integrity and effectiveness of the packaging before introducing it to the market.
The steps to achieve high-performance packaging include:
- the initial design;
- sourcing of packaging materials;
- compatibility of machines and production areas with the chosen packaging;
- stability in all environmental conditions.
The packaging must be properly sealed, undamaged, and appropriately labeled in both form and content. This includes information such as identification codes for traceability, lot number, and expiration date.
Key quality control tests for secondary packaging
Referring to secondary pharmaceutical packaging, quality control tests can be both chemical and mechanical. Packaging manufacturers, such as Eurpack, collaborate with clients to define package designs, ensure compliance with international standards, and meet agreed-upon Quality Attribute Limits (AQL).
Among the most important tests conducted on secondary packaging is the scratch resistance test (Sutherland Rub Test ASTM D5264), which evaluates the resistance of labels, folding cartons, corrugated cardboard, and other printed materials against wet or dry friction or abrasion. The reference device for this test (Ink Rub Tester) determines the resistance of ink and material under these stresses.
The ink adhesion seal test ASTM D3359 specifies the level of adhesion of a coating to a substrate. The method requires applying and removing adhesive tape to the coated surface, which has been cut previously with cross or hatch patterns depending on the coating thickness. This determines the maximum tensile force the coating can withstand before detaching.
Another compliance test for pharmaceutical secondary packaging is the shipping test (ASTM D4169), which describes the performance of the package during shipping. To ensure that packaging arrives safely at its destination, the test simulates common shipping stresses, such as dropping, impact, vibration, or crushing, to verify the integrity, reliability and safety of the packaging throughout the distribution cycle.
Control Standards in the packaging area
Pharmaceutical Quality Control conducts incoming checks on materials received for drug packaging to identify any supplier errors during the packaging release phase.
Quality control must analyze material versus shared quality standards, identifying any failure to meet essential requirements. For example, it is critical to take care of the production environment for packaging: each printing and finishing line must be segregated with dividers from others to avoid mix-ups, and cleaning must be continuously carried out and recorded on dedicated forms. In addition, personnel must be trained and updated on proper work methodologies and wear appropriate clothing based on the area of operation, as defined through a risk analysis.
ISO and GMP standards also refer to the maintenance and control of machinery to ensure proper packaging. Each supervision activity should consider product specifications, batch, and customer production needs.