The link between the right packaging choice and efficient logistics
The link between the right packaging choice and efficient logistics
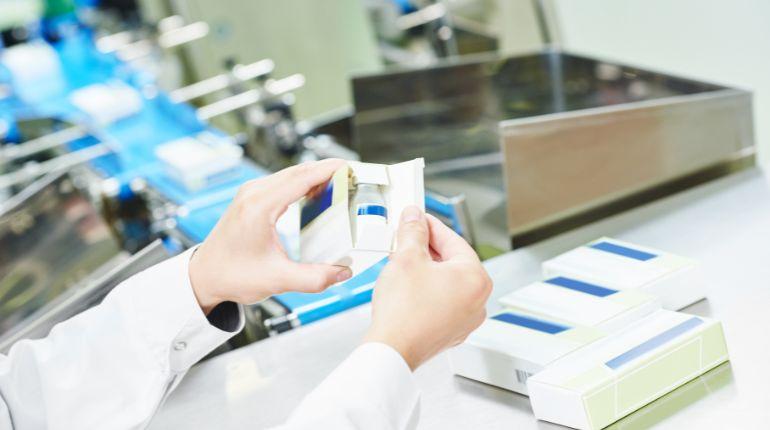
Pharmaceutical logistics is a crucial competitive lever for companies in the sector. Optimizing warehouse processes can be a long-term cost-improvement strategy for many businesses, as these are often costly and complex operations that require careful preventive analysis: market needs, transport risks, stock management, space and product storage conditions. In logistics, packaging choices are fundamental to making these flows economically sustainable: they allow efficient storage, transportation and distribution of pharmaceutical products through strategic design implementation. In this article, we will explore how logistics can be made more efficient through specific packaging solutions, from managing packaging materials in the warehouse to selecting the right design.
Strategic management of pharmaceutical packaging in the warehouse
Among the costs of the supply chain, those related to the storage of packaging materials are without a doubt the highest, because they depend on volume, space occupied, and the time they remain in the warehouse. In the pharmaceutical field, the costs of maintaining storage requirements during intermediate stages of the supply chain, as outlined in Legislative Decree no. 219/2006 (the Drug Code) and DM July 6, 1999 (Guidelines on Good Distribution Practice of Medicinal Products for Human Use), must also be considered. Temperature control systems and clean rooms with ISO 8 classification are employed to maintain suitable environmental conditions.
According to the 2023 sustainability report commissioned by Logipharma, 81% of surveyed pharmaceutical companies expect the average disposal cost of a pallet box to be €250 by 2025. To manage these costs, industry manufacturers must adopt flexible and sustainable approaches to the supply chain. The most effective ones are based on “Just in Time” principles that enable companies to stock only the material immediately needed in the packaging phase. To implement this strategy, manufacturers can allocate warehouse space to packaging material processing areas, to make logistical processes smoother and reduce the space occupied by goods while maintaining a constant production level.
Pharmaceutical companies also resort to Consignment stock, an inventory management system. This system enables them to receive a specific amount of packaging material directly in the warehouse and pay for it only when used. An agreement that optimizes warehouse and inventory costs and ensures flexibility in both material access and delivery operations between the supplier and the customer.
Transport Packaging
In the past, packaging had a more communicative than practical function. Companies designed increasingly original solutions in terms of shapes and materials, often sacrificing logistical efficiency. Nowadays, especially in the pharmaceutical industry, packaging design aims for standardization to facilitate the transport and handling of goods. A change influenced by international regulations that impose common quality requirements for consumer-targeted products. Collaboration between manufacturing and distribution industries has enabled the rethinking of a new relationship between logistics and packaging, based on the synergy between primary, secondary and tertiary packaging phases. The adoption of warehouse management or packaging design strategies, with an optimization perspective, has led to the development of “transport packaging.” This packaging, due to its design characteristics, optimizes supply chain operations and represents a cost-saving strategy. For example, it reduces the weight and space occupied by packaging in warehouses and loading units, ensuring simpler operational flows, both in the facility and during shipment. It also has positive impacts on environmental compliance: a supply chain with fewer vehicles on the road and better space management reduces resource consumption and emissions, and thus facilitates the disposal of packaging materials at the end of their life cycle thanks to the use of often eco-friendly materials.
Key Requirements for Packaging in Logistics
To achieve economic and environmental sustainability goals, it is important to consider all aspects of the product from the early design stages. For example, the lightweight and flexibility of materials, as well as the smallest possible dimensions, enable the adaptation of manpower, processing machinery and packaging lines. Regarding these aspects, the assessment of the packaging’s fragility index plays a significant role: depending on the product’s delicacy and transport risks, it is evaluated whether to use more robust and less transport-friendly packaging or optimize the design for greater convenience when risks are minimal. To create transport packaging, it is also necessary to consider its traceability along the supply chain, as required by regulatory authorities for public health and the fight against drug counterfeiting.
To make all these operational functionalities effective, it is crucial to implement an efficient synergy between design, research and development, and production phases. Pharmaceutical companies find it useful to invest in a comprehensive packaging system that includes tests to ensure that the packaging is packable and transportable, identifying any critical points and investing in potential adaptation processes based on specific needs.
To create functional packaging that interacts with all logistical operations, Eurpack has always believed in the importance of a holistic approach considering its entire life cycle. This is why Eurpack’s Packaging Development Center customizes packaging to meet the needs of all customers without neglecting the value of an economically and ethically sustainable design throughout the entire supply chain.