L’importanza del controllo qualità del packaging farmaceutico
L’importanza del controllo qualità del packaging farmaceutico
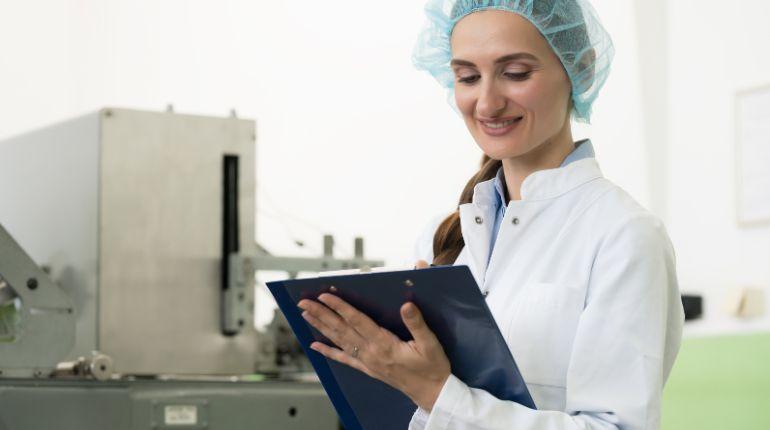
Il packaging farmaceutico riveste un ruolo importantissimo al fine di garantire l’integrità del prodotto, evitare contaminazioni da agenti esterni e assicurare la tracciabilità del farmaco lungo tutta la supply chain. Quando si progettano e si sviluppano soluzioni di packaging per il settore farmaceutico bisogna tener presente che è necessario eseguire dei test di controllo su tutte le fasi, dalla loro produzione, all’uso per il confezionamento presso le aziende farmaceutiche, in conformità agli standard dettati dai regolamenti internazionali. Oltre a garantire sempre la compliance a tali normative, un packaging di qualità controllato e validato attraverso protocolli precisi, rappresenta un elemento di ottimizzazione in termini di risorse economiche, di tempo e produttività.
In questo articolo citeremo i requisiti fondamentali di qualità di un packaging secondario e approfondiremo alcuni dei test di controllo più importanti che ne validano l’immissione in commercio.
Linee guida GMP sul controllo qualità farmaceutico del packaging
La realizzazione del packaging farmaceutico primario, secondario e terziario sottostà a numerose regole di qualità basate sulle norme ISO e GMP (Good Manufacturing Practice). Nei vari capitoli delle GMP sono esplicitate le regole da seguire per la produzione del medicinale e della sua confezione. La confezione è molto importante perché protegge i farmaci da fattori ambientali come luce, umidità e aria e impedisce la contaminazione e la manomissione del prodotto, garantendo la sua conservazione nel tempo e prevenendo i danni da trasporto lungo la catena logistica. L’altra funzione del packaging è quella di fornire informazioni chiare sul suo contenuto, sulla validità e sulla provenienza del farmaco a tutti gli operatori della supply chain fino al consumatore. Grazie ad un design chiaro e accessibile, gli utenti finali sono consapevoli di ciò che acquistano e hanno la possibilità di smaltire la confezione con facilità.
Le aziende farmaceutiche, per ottenere le più alte performances dal farmaco, sono chiamate a condurre assieme ai fornitori e ai partner molteplici test di qualità per validare l’integrità e l’efficacia della confezione prima di immettertela in commercio.
I passi per ottenere un packaging performante menzionano:
- progettazione iniziale;
- reperimento dei materiali di packaging;
- compatibilità delle macchine e delle aree di produzione con il packaging scelto;
- stabilità a qualsiasi condizione ambientale.
La confezione deve essere chiusa correttamente, non presentare danni e deve essere etichettata in maniera adeguata nella forma e nel contenuto, ossia riportare informazioni quali codice identificativo per la tracciabilità, numero di lotto e data di scadenza.
I più importanti test di controllo qualità del packaging secondario
Prendendo come riferimento il packaging farmaceutico secondario, i testi di controllo qualità del packaging possono essere di natura chimica e meccanica.
Le aziende produttrici del packaging, come Eurpack, si occupano di definire il design delle confezioni insieme ai clienti, la conformità agli standard internazionali e il soddisfacimento degli AQL (attributi di qualità) concordati.
Fra i test più importanti condotti sul packaging secondario possiamo citare il test di resistenza ai graffi (Sutherland Rub Test ASTM D5264) per valutare la resistenza di etichette, cartoni pieghevoli, cartoni ondulati e altri materiali stampati allo sfregamento o all’abrasione a umido o a secco.
Il dispositivo di riferimento per questo test (Ink Rub Tester) è in grado di determinare la durevolezza dell’inchiostro e del materiale a queste sollecitazioni.
Il test di tenuta dell’inchiostro ASTM D3359 specifica invece il grado di aderenza di un rivestimento ad un substrato. Il metodo usato è quello di applicare e rimuovere un nastro adesivo sul rivestimento su cui precedentemente sono stati applicati dei tagli (a croce o a tratteggio incrociato a seconda dello spessore del rivestimento) per determinare la massima forza di trazione che può sopportare prima di staccarsi.
Infine, un’altra verifica di conformità del packaging secondario farmaceutico è lo Shipping test (ASTM D4169) che descrive le prestazioni della confezione durante le operazioni di spedizione. Vengono dunque riprodotte alcune stimolazioni comuni durante il trasporto dei prodotti, come la caduta, l’urto, la vibrazione o la compressione. Il test mira a verificare i requisiti di integrità, affidabilità e sicurezza del packaging durante tutto il ciclo di distribuzione perché arrivi in condizioni ottimali nel sito di destinazione.
Standard di controllo nell’area di confezionamento
Il controllo qualità farmaceutico a sua volta, ricevuto il materiale che sarà utilizzato per confezionare i propri farmaci, effettua controlli “in incoming” affinché possano essere evidenziati eventuali errori del fornitore nella fase di rilascio del packaging.
Il QC inoltre deve analizzare il materiale versus gli standard di qualità condivisi individuando così il mancato rispetto di alcuni requisiti imprescindibili. Ad esempio, la cura degli ambienti in cui viene prodotto il packaging: ciascuna linea di stampa e finitura deve essere segregata con divisori dalle altre in modo da evitare frammischiamenti e la pulizia deve essere effettuata continuamente e registrata su appositi moduli. In aggiunta il personale, oltre a dover essere formato e aggiornato sulle corrette metodologie di lavoro, deve indossare un abbigliamento adeguato, diverso a seconda dell’area in cui opera e definito grazie a un’analisi del rischio.
Le norme ISO e le norme GMP fanno riferimento anche alla manutenzione e al controllo del buon funzionamento dei macchinari e di confezionamento che contribuiscono alla realizzazione del packaging. Ogni attività di supervisione deve tener conto delle specifiche del prodotto, del lotto e delle esigenze di produzione del cliente.